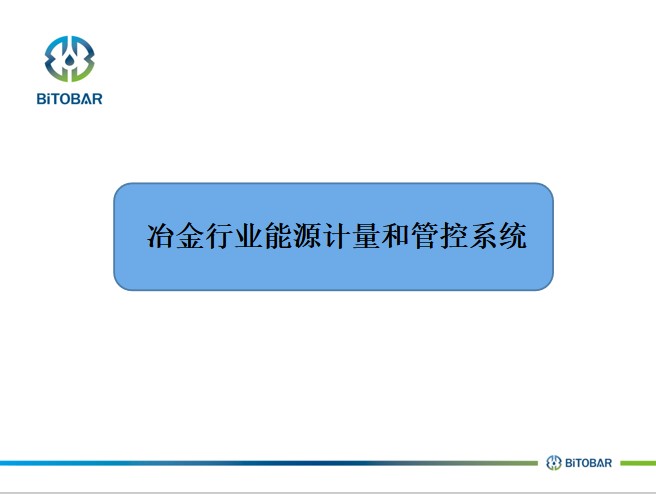
一.课题的迫切性
在高耗能行业——冶金企业,能源是生产过程中最基本的资源,确保能源系统的稳定和经济运行对企业产品的质量和企业的经济效益具有十分重要的作用。钢铁企业长期居高不下的能源消耗,不仅影响了企业的经济效益,而且严重恶化环境,不利于企业的可持续发展,是长期困扰冶金企业的难题之一。国内某年产值150多亿的矿业公司,仅由于电量计量不准以及漏计等原因,每天就与供电方计量存在上万度的误差,经济损失巨大。
冶金企业能源计量与管理系统可以作为考核生产、管理决策和指导节能的技术平台,实现对全厂耗能的总体监控,是现代企业能源管理的重要技术措施,也是大型冶金企业提高节能效益的重大技术措施。吸引了东北大学、中南大学、浙江大学、大连理工大学等高校及施耐德电气有限公司的关注,但目前行业中的能源管控系统主要还是2007年上海宝信软件股份有限公司开发的MES系统,其实现了能源管理系统的基本功能,主要包括数据的采集、记录、报警、人机界面、报表生成。
但近十年随着科技进步的发展,尤其是计量技术、物联网技术、先进控制技术的发展,冶金行业需要一套更合理精确的能源计量管控系统来满足产品质量和节能环保的要求。
二.课题的特色及内容
本课题重点关注大数据技术与控制理论在冶金行业的推广应用。
目前冶金行业的能源管控重点是在数据管理上,在控制上做得很少。究其原因,主要有以下几个方面:
- 传统的控制多为基于闭环的不需要精确建模的PID控制,在冶金行业中,很多环节的测量精度远远不够,无法实现反馈;
- 冶金行业为过程控制系统,基于机理的建模基本不可能实现,基于数据驱动的建模和控制器设计是近几年刚刚出现的技术,在行业中还没有成功案例;
- 现有的能源管控系统为软件公司开发的,缺少控制理论与控制技术的储备。
基于这些问题,本课题提出了以下内容:
- 反馈数据点的合理确定:冶金企业工况较差,在运行数十年后,其原装检测装置会出现不同程度的损坏,甚至数据完全失真,维修和更换的成本巨大,且需要停产,影响正常生产活动。而且,企业生产线经过若干年的改建扩建,在计量装置上容易形成冗余,不同的计量方案会引起10-40%的计量误差。因此,在现有拓扑结构的基础上,确定新的计量方案,主要是计量点的确定,可以降低成本,提高能源利用效率。
- 计量设备的更新:在计量点确定后,选择安装方便、计量精度更高的在线式计量装置,可以为能源管控系统提供可靠的数据支撑;
- 基于数据驱动的生产模型建立和控制器设计:从现有数据报表中提取有效数据,建立基于输入输出数据的特征模型来模拟生产过程,并以此模型为依据设计黄金分割自适应控制器来控制阀门开度等操作量,可以根据生产负荷的变化有效地动态预测煤气流量、温度、压力等关键数据的变化,实现能源的优化控制。以煤气预测为例,国内大部分钢厂的煤气柜是作保安用。建立了预测模型后,可根据工作负荷变化情况,实时预测出煤气的供需状况,指导对用户的分配方案,这样煤气柜既可保安又可作缓冲,可以提高煤气的有效利用率,减少煤气放散。
- 通过控制算法的改进提高钢铁产品的品质。 钢铁企业的冲击负荷普遍都比较大,现有的控制方式主要是人工经验加PID控制,在过渡过程造成的振荡对产品的品质有很大的影响。如果能够实现恒温或恒热量控制,可以使钢铁产品的质量提高一个或更多档次。这就需要解决现有算法在过渡过程存在的超调量和调整时间问题。而特征建模方法可以很好的解决这个问题,该算法是1992年吴宏鑫院士提出的一个工程实用性很强的控制系统建模和控制方法。以该理论为依据设计的自适应控制器包括维持跟踪、黄金分割、逻辑积分和逻辑微分四部分,解决了暂态性能、稳定性和控制精度的问题。已经成功应用于航天工程、航天地面工程、过程控制等多个系统,如飞船的再入、飞船的交会对接、药厂的温度控制等,为复杂的生产控制提供了一种新型的中国人自己开发的控制方法。
- 用能优化分析 :在企业总利润最高,能耗最低的目标下指导企业改善能源结构和产品结构;
- 能源预测与分析用能优化分析:根据历史数据,采用预测方法,预测各种能源的未来消费趋势,合理安排采购和生产活动。
- 提供各种管理人员需要的报表:根据权限,由用户自行生成所需报表并打印输出。方便管理人员及时掌握各类信息。
三.课题的具体技术路线
根据初步调研,总结冶金行业的能源管控基本包括如下几方面:
①供配电系统;②给排水系统,包括输水系统、排水泵站、消防系统等; ③动力系统:包括煤气加压站、煤气混合站、煤气柜、放散塔、燃气管网系统、蒸汽系统、氧气氮气等输配系统。
设计能源管控系统的基本目标是:由能源中心进行集中监控,实现变电所、变电室等供配电区域;煤气柜、煤气加压站、煤气放散、煤气混合等煤气区域;排水泵站等水区域;空压站等区域的全自动化生产,对能源平衡进行预测和及时调整,以减少煤气放散,增加转炉煤气回收,并对异常运行情况进行快速处理。
针对马鞍山钢铁厂的具体情况,考虑先从目前急需解决的煤气计量及管控方面入手。具体实施方案如下:
- 确定数据采集方案,包括测量点的拓扑选择及不同数据的采集方式(周期采集或中断采集等);
- 整理数据,包括数据的分类和管理权限的确定,数据分类主要有实时数据、短时数据、统计数据、历史数据、记录等;管理权限主要是根据部门不同,界定可以查看到的生产数据,及对数据进行处理的指导方案等;
- 特征模型的建立及黄金分割自适应控制器的设计,实现煤气流量的自动调节,并通过算法的预测性和自适应性提高煤气品质,进而提升钢铁产品的品质;
- 安全性保证,主要是各种报警、故障的排除、记录和分析等。
四.课题效果
保守预期,可使煤气的管网损失从现在的40%降低到20%;提高能源的运行管理效率,实现全自动控制后,可使日常管理成本降低50%;能源实时平衡能力提高30%-80%,大大减少煤气放散量;能源管理系统的综合效益预期在5元/吨钢左右。